Fertigung von VMZINC
Der Werkstoff hinter der Marke · Ein Überblick über die Herstellung von VMZINC
Geschichte der Zinkherstellung
Bereits in der Antike wurde Zinkerz zur Herstellung von Messing genutzt. Der Fertigungsprozess, bei dem das Erz erhitzt wurde, war schwierig, da Zink bereits bei Temperaturen unter 1000°C verdampft. Ab dem 12. Jahrhundert begann in Indien die Zinkproduktion, und das Wissen darüber verbreitete sich, sodass auch in China ab dem 17. Jahrhundert Zink erzeugt wurde. In mittelalterlichem Europa musste das Metall jedoch noch importiert werden. Erst 1743 gelang es in Grossbritannien, Zink in einem Schmelzofen herzustellen. Einige Jahrzehnten später entstand auch in Kärnten, Schlesien und Belgien eine zunächst kleine Zinkproduktion. 1805 gelang es schließlich erstmals, Zink zu walzen, was seinen Einsatz im Bauwesen ermöglichte.
Zinkherstellung heute
Zink ist ein natürlich vorkommendes Element, das als Erz abgebaut und zu Feinzink weiterverarbeitet wird. Heute kommt bei der Zinkproduktion nicht mehr der Schmelzofen zum Einsatz, sondern das Verfahren der Elektrolyse. Nach einem Röst- und Laugvorgang wird Feinzink durch elektrischen Strom an einer Kathode abgeschieden. Das durch Elektrolyse gewonnene Zink hat einen Reinheitsgrad von 99,995%.
Die Herstellung erfolgt in den folgenden Schritten:
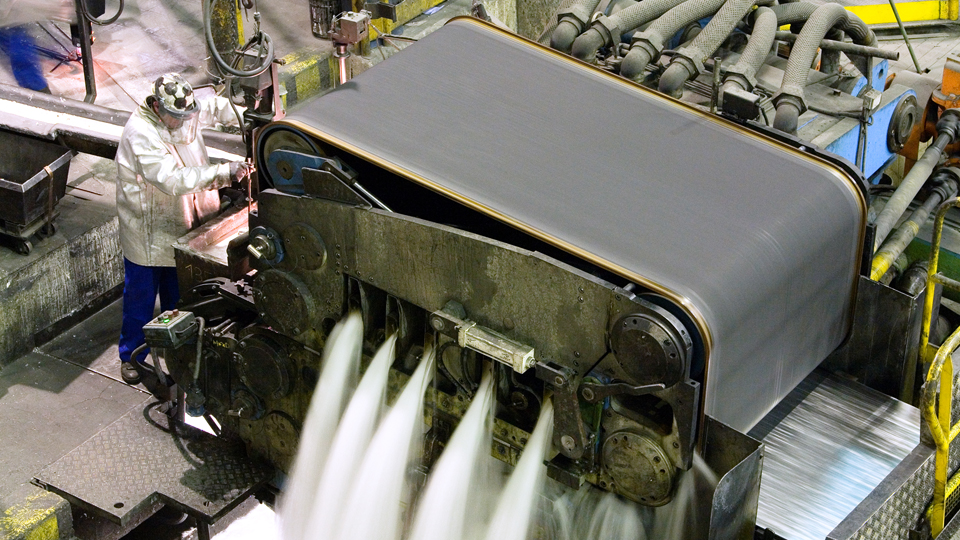
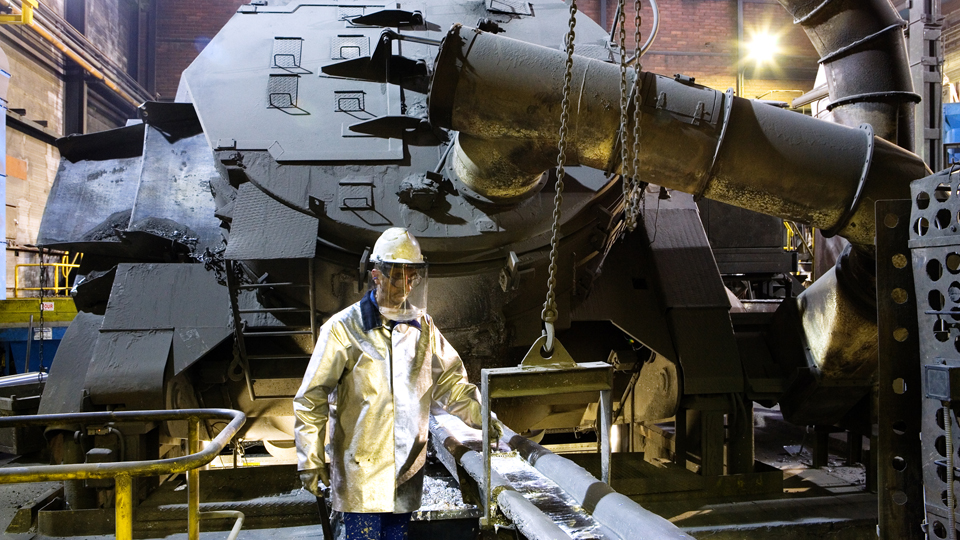
Herstellen der Legierung
Die Produktion von VMZINC in den gängigen Formen wie Blechen und Bändern erfolgt in zwei Walzwerken in Frankreich. In der ersten Fertigungsphase nach der Feinzinkherstellung werden dem reinen Zink Kupfer und Titan hinzugefügt. Die mechanisch-technologischen Eigenschaften des VMZINC-Titanzinks übertreffen die von reinem Zink deutlich. Nach dem Schmelzen wird die noch flüssige Legierung im kontinuierlichen Giesswalzverfahren weiterverarbeitet.
Walzen
Ein Gussstrang mit einer Dicke von 16 mm wird erzeugt. Der Abkühlungsprozess in der Anlage sorgt für eine feine, gleichmäßige und fest strukturierte Materialoberfläche. Dieser Gussstrang wird anschließend in mehreren Walzgängen auf die gewünschte Dicke, beispielsweise 0,7 oder 0,8 mm, reduziert. Dabei werden Temperatur, Geschwindigkeit und Reduktionsrate kontinuierlich überwacht, um die gewünschten Eigenschaften des Endprodukts zu gewährleisten.
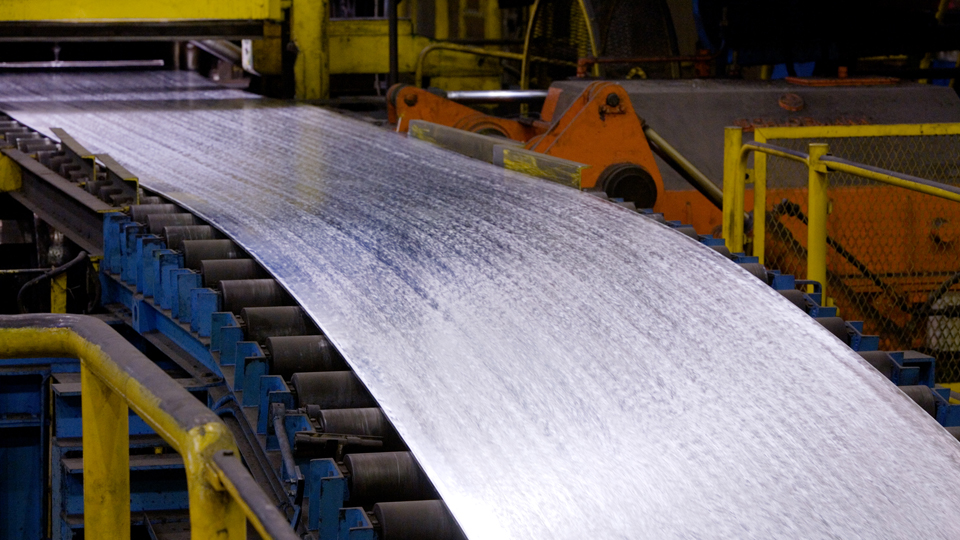
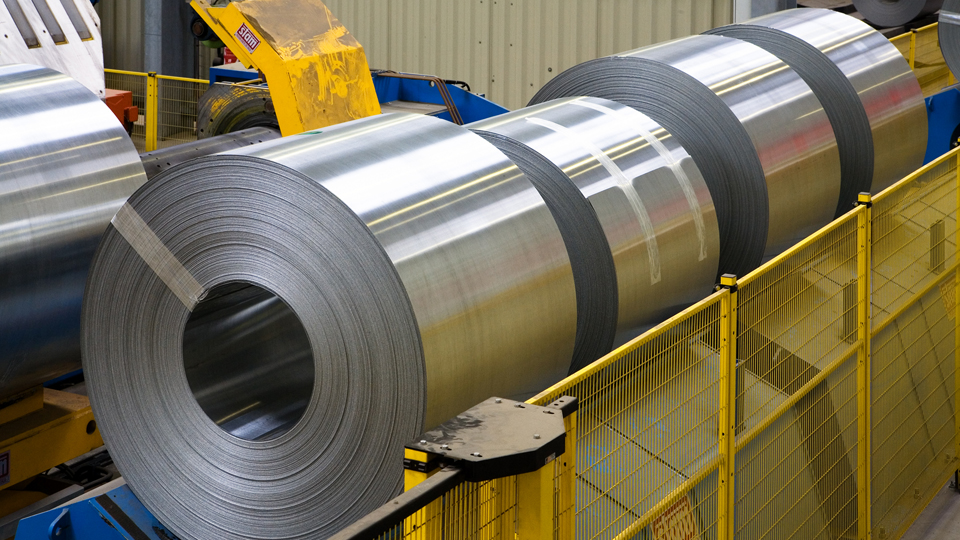
Erzeugung von Blechen und Bändern
Dieses hochmoderne Fertigungsverfahren sorgt für eine konstant hohe Qualität mit minimalen Dickentoleranzen. Die gewonnenen Bänder werden anschließend auf speziell dafür entwickelten Maschinen längs und/oder quer geschnitten und gestreckt, um sie in die handelsüblichen Formen von Bändern und Blechen zu bringen.
Für die Herstellung von vorbewitterten und gravierten Oberflächen erfolgt ein weiterer Schritt, bei dem auf der Zinkoberfläche durch eine chemische Reaktion eine künstliche Patina gebildet wird.
Qualitätsüberwachung
Während des gesamten Produktionsprozesses werden sämtliche Eigenschaften des Materials kontinuierlich überwacht, um sicherzustellen, dass sie den Anforderungen der Norm EN 988 entsprechen. Dies umfasst sowohl die chemische Zusammensetzung als auch die mechanischen Eigenschaften des Zinks, um eine gleichbleibend hohe Qualität zu gewährleisten. Darüber hinaus wird der gesamte Produktionsablauf regelmäßig überprüft, um die Einhaltung der hohen Standards zu bestätigen.
Die effiziente Steuerung und Qualitätssicherung des Produktionsprozesses sind durch die Zertifizierung nach ISO 9001 dokumentiert. Diese Zertifizierung belegt nicht nur die konsequente Umsetzung von Qualitätsmanagementrichtlinien, sondern auch das Engagement des Unternehmens für kontinuierliche Verbesserung und Kundenzufriedenheit.